Straight-cut gears might not be the most glamorous part of a machine, but they are absolutely crucial in making things work smoothly. From cars to industrial equipment, they play an integral role in various mechanical systems. This guide will explore everything you need to know about straight-cut gears, including their design, functionality, and applications.
What Are Straight-Cut Gears?
Often known as spur gears, these are the simplest type of gear, have straight teeth that are cut parallel to the axis of rotation. Unlike helical gears, which have angled teeth, straight-cut gears’ teeth engage directly, providing a straightforward and efficient way to transmit motion and force between two rotating shafts.
How Do They Work?
Straight-cut gears operate by interlocking their teeth. As two gears engage, the teeth of one gear push against the other, resulting in rotational movement. This transfer of force allows one gear to drive the other. The efficiency of this gear type comes from the direct contact between the teeth, which allows for precise motion transfer. However, this direct contact can also lead to increased noise and wear.
Key Features
Straight-cut gears are characterized by their simple design, which features teeth cut along a straight, parallel line. This simplicity allows for ease of manufacturing and cost-effectiveness. They typically consist of various materials, such as steel, brass, and even plastic, depending on the application requirements. The teeth are evenly spaced and have a uniform profile, which is crucial for efficient power transmission.
Types of Straight-Cut Gears
- Spur Gears: The most common type of straight-cut gears, spur gears have teeth that are cut straight and parallel to the axis of the gear. They are used in a variety of applications where efficiency and simplicity are desired.
- Rack and Pinion Systems: A combination of a straight-cut gear (pinion) and a linear gear (rack). This gear system transforms rotational movement into linear force. It is often found in applications like steering mechanisms and various types of machinery where precise, efficient power transfer is needed.
Advantages
- Simplicity in Design: Straight-cut gears have a simple design, making them easy to manufacture and maintain.
- Cost-Effectiveness: Due to their straightforward construction, these gears are less expensive to produce than more complex gears like helical or bevel gears.
- High Efficiency: They provide efficient power transmission with minimal losses, especially in low-speed applications.
Disadvantages
- Noise: Straight-cut gears tend to be noisy because of the abrupt engagement of teeth. This is especially noticeable at high speeds.
- Stress and Wear: The direct meshing of teeth leads to higher stress on each tooth, potentially causing faster wear and tear compared to helical gears.
Applications
Straight-cut gears are favored in many applications because of their simplicity and effectiveness.
- Automotive Transmissions: In high-performance vehicles, these are favored for their ability to handle high torque loads, despite the noise.
- Industrial Machinery: They are often used in conveyor systems, printing presses, and other machinery where precise motion control is crucial.
- Robotics: The straightforward design makes them suitable for robotics, where reliable, precise movement is necessary.
Straight-Cut Gears vs. Helical Gears
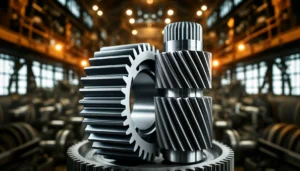
The primary difference between straight-cut gears and helical gears lies in the shape and orientation of the teeth. Straight-cut gears have teeth that are parallel to the axis of rotation, while helical gears have angled teeth that gradually engage. This difference results in smoother, quieter operation for helical gears, but also more complexity in manufacturing. Straight-cut gears are preferred when simplicity, cost, and efficiency take precedence over noise reduction.
Materials Used for Straight-Cut Gears
Common materials include:
- Steel: provides the strength and durability necessary for heavy-duty uses.
- Brass: Used for gears that require resistance to corrosion and smooth operation.
- Plastic: Employed in lightweight, low-load applications, such as in household appliances or toys.
The choice of material affects the gear’s performance, durability, and cost, making it an important factor in gear selection.
Design and Manufacturing
Straight-cut gears are typically manufactured using processes like hobbing, milling, or grinding. The design process focuses on ensuring the teeth are evenly spaced and have the correct profile to facilitate efficient power transmission. Precision is crucial in manufacturing to avoid issues like misalignment and excessive noise.
Maintenance and Care
Proper maintenance includes regular lubrication to minimize friction and wear. It’s also important to inspect the gear teeth periodically for signs of damage, such as pitting or chipping. Early detection of wear can prevent more serious damage to the gear system.
How to Choose the Right Straight-Cut Gear
When selecting a straight-cut gear, consider factors such as the load it needs to handle, the speed of operation, and the environment in which it will be used. High-load applications may require steel gears, while low-load, noise-sensitive environments might benefit from plastic gears. Additionally, the gear’s size and tooth profile should match the application’s requirements for optimal performance.
Innovations and Future of Straight-Cut Gears
Advances in gear manufacturing technology, such as computer numerical control (CNC) machining and 3D printing, have made it easier to produce high-precision straight-cut gears. In modern mechanical systems, these gears are often integrated into more complex arrangements, improving overall efficiency and performance.
Conclusion
Straight-cut gears, with their simple yet effective design, are indispensable components in many mechanical systems. Despite their noise and wear issues, their efficiency, ease of manufacturing, and cost-effectiveness make them a popular choice in various industries. Understanding their characteristics, advantages, and limitations can help in selecting the right gear for any application.
FAQs
Why are straight-cut gears noisy?
The noise is due to the abrupt engagement of teeth during rotation, which creates impact forces and vibrations.
Can straight-cut gears handle high-speed applications?
Yes, but they may become very noisy at high speeds. Proper lubrication and material choice can mitigate some of this noise.
What is the difference between straight-cut and spur gears?
The terms “spur gear” and “straight-cut gear” are often used interchangeably, both referring to gears with straight, parallel teeth that transmit power efficiently.
Are straight-cut gears more durable than helical gears?
Not necessarily. Helical gears tend to have a longer lifespan due to their smoother engagement and distribution of load across multiple teeth.
How do I reduce the noise in straight-cut gear systems?
Proper lubrication, precise alignment, and the use of materials designed to dampen vibrations can help reduce noise levels.